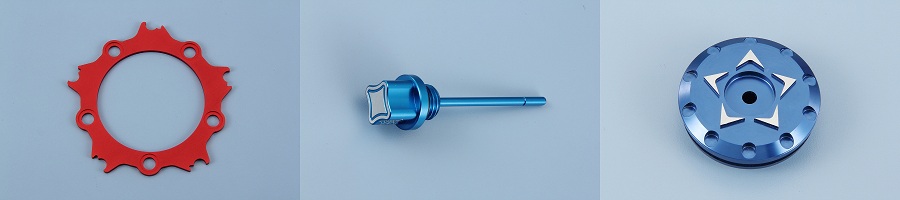
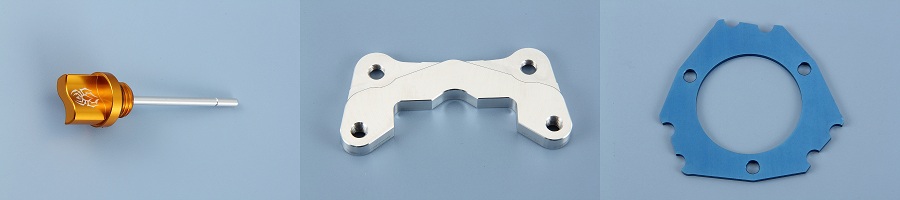
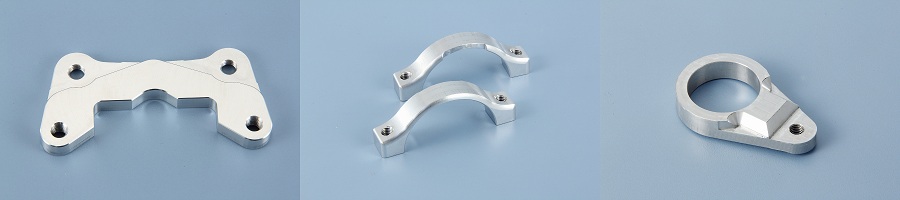
治具研發
治具研發是指研發和製造各種治具治具研發是指研發和製造各種治具,用於生產過程中固定、支撐、夾持、定位和檢測產品,以確保產品生產過程中的精度和穩定性。治具研發的目的是為了提高產品生產的效率和質量,減少生產過程中的人工和時間成本。
治具研發需要擁有相關的技術和設備,例如CAD/CAM軟件、加工中心、銑床、磨床等。治具研發的過程包括以下幾個步驟:
設計:根據產品設計要求,設計適合的治具,包括夾具、定位器、檢測治具等。
模擬:使用CAD/CAM軟件進行治具設計的模擬和優化,確定治具的尺寸和形狀。
製造:使用加工中心、銑床、磨床等設備進行治具的加工和製造,確保治具的精度和穩定性。
調試:將治具安裝到生產線上,進行調試和測試,確定治具的正確性和可靠性。
治具研發需要考慮到產品的設計要求和生產過程的實際需求,同時需要進行嚴格的品質控制和檢驗,以確保生產出高品質、高精度的治具,滿足生產需求。治具研發可以幫助企業提高生產效率和質量,降低生產成本,提高企業的競爭力。
治具研發在現代制造業中扮演著極為重要的角色。這些治具不僅可以提高生產效率,還可以確保生產過程中的產品質量和一致性。以下是有關治具研發的更多信息:
-
治具的種類:治具可以分為不同種類,包括夾具、定位治具、夾持治具、檢測治具、組裝治具等。每種治具都有其特定的功能,用於不同的生產過程。
-
設計和優化:治具的設計是一個關鍵步驟,需要考慮到產品的幾何形狀、尺寸、材料特性以及生產過程的需求。CAD/CAM軟件在治具設計中扮演著重要角色,可以進行模擬和優化,以確保治具的正確性和效率。
-
材料選擇:治具的材料選擇直接影響其性能和耐用性。常見的治具材料包括鋼、鋁、塑料和特殊合金,根據具體需求進行選擇。
-
製造過程:治具的製造過程包括數控加工、鍛造、焊接、熱處理和表面處理等步驟。這些過程需要高度技術和精密設備,以確保治具的品質和性能。
-
調試和測試:完成治具後,需要進行調試和測試,以確保其正確性和可靠性。這包括確保治具的定位、夾持和檢測功能正常運行。
-
品質控制:品質控制是治具研發過程中的關鍵步驟。治具必須符合特定的規格和標準,以確保生產過程中的一致性和可靠性。
治具研發的成功可以幫助企業提高生產效率,降低生產成本,同時提高產品質量和一致性。這對於在競爭激烈的市場中取得成功至關重要。因此,治具研發是現代制造業中不可或缺的一部分,對提高企業競爭力和生產效率至關重要。
Fixture research and development refers to the development and manufacture of various fixtures, which are used to fix, support, clamp, position and detect products during the production process to ensure accuracy and stability during the product production process. The purpose of fixture research and development is to improve the efficiency and quality of product production and reduce labor and time costs in the production process.
Jig research and development requires relevant technologies and equipment, such as CAD/CAM software, machining centers, milling machines, grinders, etc. The process of fixture development includes the following steps:
Design: According to product design requirements, design suitable fixtures, including fixtures, positioners, detection fixtures, etc.
Simulation: Use CAD/CAM software to simulate and optimize the jig design and determine the size and shape of the jig.
Manufacturing: Use machining centers, milling machines, grinders and other equipment to process and manufacture fixtures to ensure the accuracy and stability of the fixtures.
Debugging: Install the fixture on the production line, conduct debugging and testing to determine the correctness and reliability of the fixture.
Fixture research and development needs to take into account the design requirements of the product and the actual needs of the production process. At the same time, strict quality control and inspection are required to ensure the production of high-quality, high-precision fixtures to meet production needs. Fixture research and development can help enterprises improve production efficiency and quality, reduce production costs, and improve the competitiveness of enterprises.
Fixture research and development plays an extremely important role in modern manufacturing. These fixtures not only improve production efficiency, but also ensure product quality and consistency during the production process. Here is more information about fixture development:
Types of fixtures: Fixtures can be divided into different types, including fixtures, positioning fixtures, clamping fixtures, testing fixtures, assembly fixtures, etc. Each fixture has its specific function and is used in different production processes.
Design and optimization: The design of the fixture is a critical step that takes into account the product's geometry, size, material properties, and production process needs. CAD/CAM software plays an important role in jig design and can perform simulation and optimization to ensure the accuracy and efficiency of the jig.
Material selection: The material selection of the fixture directly affects its performance and durability. Common jig materials include steel, aluminum, plastic and special alloys, selected according to specific needs.
Manufacturing process: The manufacturing process of the jig includes steps such as CNC machining, forging, welding, heat treatment and surface treatment. These processes require a high degree of technology and precision equipment to ensure the quality and performance of the fixtures.
Debugging and testing: After the fixture is completed, it needs to be debugged and tested to ensure its correctness and reliability. This includes ensuring that the fixture’s positioning, clamping and inspection functions are functioning properly.
Quality control: Quality control is a key step in the fixture development process. Fixtures must meet specific specifications and standards to ensure consistency and reliability in the production process.
The success of fixture research and development can help companies improve production efficiency, reduce production costs, and at the same time improve product quality and consistency. This is critical to success in a highly competitive market. Therefore, fixture research and development is an indispensable part of modern manufacturing and is crucial to improving corporate competitiveness and production efficiency.