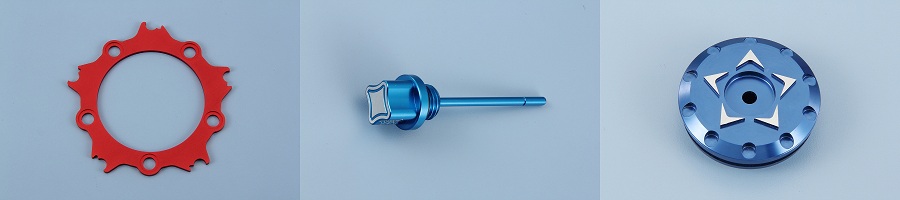
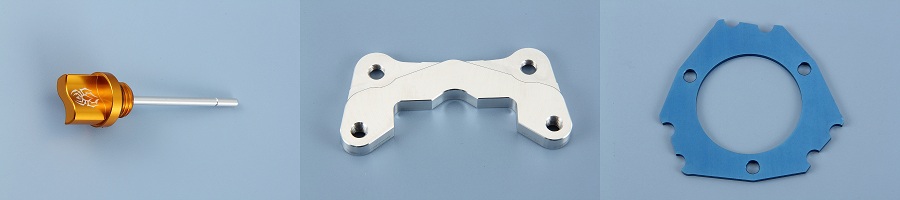
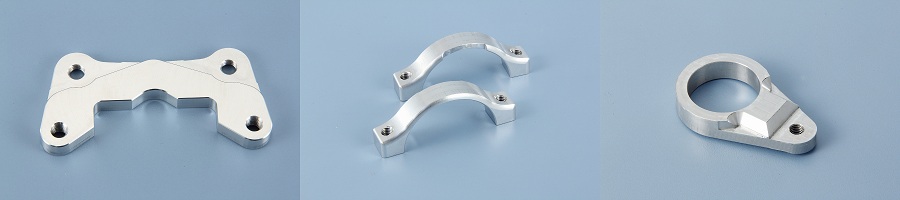
零件生產
零件生產是指生產各種機械零件、汽車零件、機車零件等產品的過程零件生產是指將各種機械零件、汽車零件、機車零件等產品加工和生產出來的過程。零件生產通常需要使用高精度和高質量的加工技術和設備,例如CNC機床、銑床、車床、磨床、鑽床等。
在零件生產的過程中,需要按照產品設計圖紙和工藝要求進行加工和生產,通常包括以下幾個步驟:
材料選擇:根據產品要求和工藝要求,選擇適合的材料進行加工,例如金屬、塑料、陶瓷等。
設備選擇:根據產品設計和加工要求,選擇適合的加工設備,例如銑床、車床、磨床等。
刀具選擇:根據產品材料和加工要求,選擇適合的刀具進行加工,例如銑刀、鑽頭、切削刀等。
加工工藝:根據產品設計和加工要求,確定加工工藝和加工路徑,例如鑽孔、銑削、切削等。
檢測和驗證:在零件加工完成後,進行檢測和驗證,確認零件的尺寸、精度、表面質量等是否符合要求。
零件生產需要擁有相應的加工技術和設備,並且需要進行嚴格的品質控制和檢驗,以確保生產出高品質、高精度的產品,滿足客戶的需求。
零件生產(CNC銑床加工):現代製造業的關鍵技術
引言
隨著科技的不斷進步,製造業正處於一個充滿挑戰和機遇的時代。電子產品、汽車、航空航天和醫療設備等行業對高精度、高品質零件的需求不斷增加,而CNC銑床加工正是滿足這些需求的重要技術之一。本文將深入介紹CNC銑床加工技術,探討其在現代製造業中的關鍵作用,以及其對產業的重要性。
第一部分:CNC銑床加工的基本概念
CNC(電腦數控)銑床加工是一種高度精密的加工技術,它利用電腦控制的銑床來切削、雕刻和鑽孔金屬、塑料和其他材料,以製造各種不同形狀和大小的零件。與傳統的手工或半自動加工方法相比,CNC銑床加工具有以下優勢:
高精度:CNC銑床能夠實現極高的加工精度,通常達到微米級別。這使得它成為製造高品質產品的理想選擇,尤其是在醫療設備和航空航天等領域。
高效率:相對於手工加工或半自動加工,CNC銑床能夠更快速地完成任務,減少生產周期並提高生產效率。
多樣化能力:CNC銑床可以處理多種不同的材料,包括金屬、塑料、陶瓷等,並製造各種形狀和大小的零件。
自動化:CNC銑床的自動化控制系統能夠實現高度自動化的生產過程,減少操作員的參與,降低人工成本。
第二部分:CNC銑床加工的應用
CNC銑床加工廣泛應用於各種不同的行業和領域,以下是一些主要的應用領域:
汽車製造:汽車行業需要大量的精密零件,如引擎部件、變速器、輪轂等,CNC銑床加工在汽車製造中發揮了關鍵作用,確保產品的質量和性能。
航空航天:在航空航天領域,零件的精密度和耐久性至關重要。CNC銑床加工用於製造飛機發動機、機翼組件、螺栓等,確保飛行器的安全和性能。
醫療設備:醫療設備需要高精度的零件,以確保醫療設備的準確性和可靠性。CNC銑床加工用於製造各種醫療設備,如醫用器械、人工假髖關節、心臟起搏器等。
電子產品:現代電子產品的小型化和高性能要求高精度的零件。CNC銑床加工用於製造電子產品的外殼、連接器、散熱器等。
模具製造:模具是製造塑料零件和金屬零件的關鍵工具,CNC銑床加工用於製造各種模具,以實現高精度和高效率的生產。
第三部分:CNC銑床加工的技術特點
CNC銑床加工的技術特點包括以下幾個方面:
數控系統:CNC銑床配備了先進的數控系統,操作員可以通過電腦控制加工過程,設定刀具的運動軌跡、切削速度、進給速度等參數,實現高度精確的加工。
刀具選擇:不同的零件需要不同的刀具,CNC銑床可以根據加工需求選擇合適的刀具,包括立銑刀、球頭銑刀、鑽孔刀具等。
材料選擇:CNC銑床可以處理各種不同的材料,包括鋼、鋁、銅、塑料等,並根據材料的特性調整加工參數。
自動化加工:CNC銑床通常配備自動換刀系統,可以在加工過程中自動更換刀具,提高生產效率。
監控和檢測:CNC銑床可以配備監控和檢測系統,實時監測加工過程,檢測零件的尺寸和表面質量,確保產品符合要求。
第四部分:CNC銑床加工的未來趨勢
隨著科技的不斷發展,CNC銑床加工也在不斷演進,以下是未來趨勢的一些方向:
智能化和自動化:未來的CNC銑床將更加智能化,能夠實現自動調整加工參數、自動故障檢測和自動修復等功能,減少人工干預。
數據分析和預測維護:CNC銑床將能夠收集大量的加工數據,通過數據分析和機器學習技術預測設備故障,實現預測性維護。
高速切削和高效能刀具:未來的CNC銑床將具備更高的切削速度和更長的刀具壽命,提高加工效率和節省成本。
結論
CNC銑床加工是現代製造業的一個關鍵技術,它為各種行業提供了高精度、高效率的零件生產解決方案。隨著科技的不斷發展,CNC銑床加工技術將不斷演進,為製造業帶來更多的機遇和挑戰。無論是在汽車、航空航天、醫療設備還是電子產品製造領域,CNC銑床加工都將繼續發揮關鍵作用,推動產業的不斷發展和進步。
第五部分:環保和可持續性
環保和可持續性是現代製造業的重要關注點之一,CNC銑床加工也不例外。未來的CNC銑床將更加關注節能和減少廢棄物的目標。一些趨勢包括:
節能設計:新一代CNC銑床將採用節能設計,包括更高效的電動機、節能的冷卻系統和智能能源管理,以減少能源消耗。
循環經濟:CNC銑床加工過程產生的廢棄物將被更廣泛地回收和再利用,以減少對自然資源的需求。
綠色材料:製造業將越來越多地使用綠色材料,這些材料具有更低的環境影響,並且可以更容易地在製造過程中加工。
第六部分:教育和培訓
CNC銑床加工需要具備特定技能和知識的操作員。未來,將有更多的教育和培訓機會來培養這些技能。一些趨勢包括:
虛擬培訓:虛擬班和模擬器將用於培訓操作員,以減少實際機器的運行時間和成本。
在線學習:網絡上的在線課程和資源將為有興趣學習CNC銑床加工的人提供方便的途徑。
合作學習:製造企業將更加積極地與教育機構合作,提供實習和學徒培訓機會。
第七部分:全球化和競爭
製造業是全球化的,競爭激烈。CNC銑床加工企業將需要擴大國際市場,不僅在本國市場競爭,還需應對來自其他國家的競爭。一些趨勢包括:
國際合作:跨國合作和合資企業將有助於擴大市場份額和共享技術知識。
全球供應鏈:製造企業將更加依賴全球供應鏈,以確保原材料的穩定供應和成本效益。
品質和創新:高品質的產品和不斷創新的能力將成為競爭的關鍵因素。
結語
CNC銑床加工技術在現代製造業中具有不可或缺的地位,它為高精度、高效率的零件生產提供了解決方案,同時也面臨著不斷發展和變革的挑戰。未來,我們可以預期CNC銑床加工技術將繼續發展,並在環保、教育和全球化等方面帶來更多的創新和機遇。無論是在製造業的哪個領域,CNC銑床加工都將繼續發揮著重要作用,推動產業的不斷進步。
Parts production refers to the process of producing various mechanical parts, automobile parts, motorcycle parts and other products. Parts production refers to the process of processing and producing various mechanical parts, automobile parts, motorcycle parts and other products. Part production usually requires the use of high-precision and high-quality processing technology and equipment, such as CNC machine tools, milling machines, lathes, grinders, drilling machines, etc.
In the process of parts production, processing and production need to be carried out in accordance with product design drawings and process requirements, which usually includes the following steps:
Material selection: According to product requirements and process requirements, select suitable materials for processing, such as metal, plastic, ceramics, etc.
Equipment selection: According to product design and processing requirements, select suitable processing equipment, such as milling machines, lathes, grinders, etc.
Tool selection: According to the product material and processing requirements, select suitable tools for processing, such as milling cutters, drill bits, cutting knives, etc.
Processing technology: According to product design and processing requirements, determine the processing technology and processing paths, such as drilling, milling, cutting, etc.
Inspection and verification: After the parts are processed, inspection and verification are carried out to confirm whether the size, accuracy, surface quality, etc. of the parts meet the requirements.
Parts production requires corresponding processing technology and equipment, and strict quality control and inspection are required to ensure the production of high-quality, high-precision products to meet customer needs.
Parts production (CNC milling): a key technology for modern manufacturing
introduction
With the continuous advancement of science and technology, the manufacturing industry is in an era full of challenges and opportunities. Industries such as electronics, automotive, aerospace, and medical equipment are increasingly demanding high-precision, high-quality parts, and CNC milling machine processing is one of the important technologies to meet these needs. This article will provide an in-depth introduction to CNC milling machine processing technology, explore its key role in modern manufacturing, and its importance to the industry.
Part 1: Basic concepts of CNC milling machine processing
CNC (computer numerical control) milling is a highly precise machining technology that uses computer-controlled milling machines to cut, engrave and drill metal, plastic and other materials to create parts of a variety of shapes and sizes. Compared with traditional manual or semi-automatic processing methods, CNC milling machine processing has the following advantages:
High precision: CNC milling machines are capable of extremely high machining accuracy, often down to the micron level. This makes it ideal for manufacturing high-quality products, especially in areas such as medical devices and aerospace.
High efficiency: Compared with manual processing or semi-automatic processing, CNC milling machines can complete tasks faster, reduce production cycles and improve production efficiency.
Diversified capabilities: CNC milling machines can handle many different materials, including metals, plastics, ceramics, etc., and create parts of various shapes and sizes.
Automation: The automated control system of CNC milling machines can achieve a highly automated production process, reduce operator participation, and reduce labor costs.
Part 2: Application of CNC milling machine processing
CNC milling machine processing is widely used in a variety of different industries and fields. Here are some of the main application areas:
Automobile manufacturing: The automobile industry requires a large number of precision parts, such as engine parts, transmissions, wheels, etc. CNC milling machine processing plays a key role in automobile manufacturing to ensure product quality and performance.
Aerospace: In the aerospace industry, part precision and durability are critical. CNC milling machine processing is used to manufacture aircraft engines, wing components, bolts, etc. to ensure the safety and performance of aircraft.
Medical Equipment: Medical equipment requires high-precision parts to ensure the accuracy and reliability of the medical equipment. CNC milling machine processing is used to manufacture various medical equipment, such as medical instruments, artificial hip joints, pacemakers, etc.
Electronic products: The miniaturization and high performance of modern electronic products require high-precision parts. CNC milling machines are used to manufacture housings, connectors, radiators, etc. for electronic products.
Mold manufacturing: Molds are key tools for manufacturing plastic parts and metal parts. CNC milling machine processing is used to manufacture various molds to achieve high-precision and high-efficiency production.
Part Three: Technical Characteristics of CNC Milling Machine Processing
The technical characteristics of CNC milling machine processing include the following aspects:
CNC system: CNC milling machines are equipped with advanced CNC systems. The operator can control the processing process through the computer and set parameters such as the tool's motion trajectory, cutting speed, and feed speed to achieve highly accurate processing.
Tool selection: Different parts require different tools. CNC milling machines can select appropriate tools according to processing needs, including end mills, ball end mills, drilling tools, etc.
Material selection: CNC milling machines can handle a variety of different materials, including steel, aluminum, copper, plastic, etc., and adjust processing parameters according to the characteristics of the material.
Automated processing: CNC milling machines are usually equipped with automatic tool changing systems, which can automatically change tools during processing to improve production efficiency.
Monitoring and detection: CNC milling machines can be equipped with monitoring and detection systems to monitor the processing process in real time, detect the size and surface quality of parts, and ensure that the product meets the requirements.
Part 4: Future Trends of CNC Milling Machine Processing
With the continuous development of technology, CNC milling machine processing is also constantly evolving. The following are some directions of future trends:
Intelligence and automation: Future CNC milling machines will be more intelligent, capable of automatically adjusting processing parameters, automatic fault detection and automatic repair, reducing manual intervention.
Data analysis and predictive maintenance: CNC milling machines will be able to collect large amounts of processing data, predict equipment failures through data analysis and machine learning technology, and achieve predictive maintenance.
High-speed cutting and high-performance tools: Future CNC milling machines will have higher cutting speeds and longer tool life, improving processing efficiency and saving costs.
in conclusion
CNC milling machine processing is a key technology in modern manufacturing, which provides high-precision and efficient part production solutions for various industries. With the continuous development of science and technology, CNC milling machine processing technology will continue to evolve, bringing more opportunities and challenges to the manufacturing industry. Whether in the automotive, aerospace, medical equipment or electronics manufacturing fields, CNC milling machine processing will continue to play a key role in promoting the continuous development and progress of the industry.
Part Five: Environmental Protection and Sustainability
Environmental protection and sustainability are one of the important concerns of modern manufacturing, and CNC milling machine processing is no exception. Future CNC milling machines will focus even more on energy conservation and waste reduction goals. Some trends include:
Energy-saving design: The new generation of CNC milling machines will feature energy-saving designs, including more efficient motors, energy-saving cooling systems and smart energy management to reduce energy consumption.
Circular economy: Waste generated by CNC milling processes will be more widely recycled and reused to reduce demand on natural resources.
Green materials: Manufacturing will increasingly use green materials, which have a lower environmental impact and can be more easily processed in the manufacturing process.
Part Six: Education and Training
CNC milling requires operators with specific skills and knowledge. In the future, there will be more education and training opportunities to develop these skills. Some trends include:
Virtual training: Virtual classes and simulators will be used to train operators to reduce actual machine running time and costs.
Online Learning: Online courses and resources on the Internet will provide a convenient way for those interested in learning CNC milling.
Collaborative learning: Manufacturing companies will be more active in partnering with educational institutions to provide internship and apprenticeship opportunities.
Part Seven: Globalization and Competition
Manufacturing is globalized and competition is fierce. CNC milling machine processing companies will need to expand the international market and not only compete in their home market, but also deal with competition from other countries. Some trends include:
International Cooperation: Cross-border cooperation and joint ventures will help expand market share and share technological knowledge.
Global supply chain: Manufacturing companies will rely more on global supply chains to ensure stable supply of raw materials and cost-effectiveness.
Quality and innovation: High-quality products and the ability to continuously innovate will become key factors in competition.
Conclusion
CNC milling machine processing technology plays an indispensable role in modern manufacturing. It provides solutions for high-precision and high-efficiency parts production, and at the same time faces the challenges of continuous development and change. In the future, we can expect that CNC milling machine processing technology will continue to develop and bring more innovation and opportunities in environmental protection, education, and globalization. No matter which field of manufacturing you are in, CNC milling machine processing will continue to play an important role in promoting the continuous progress of the industry.